Quality Assurance
Policy and Strategy
Pursuant to its global Quality Policy, the Kyowa Kirin Group is committed to providing products and services that earn the satisfaction and trust of its customers.
Kyowa Kirin Group Quality Policy
Revised on November 1, 2023
1. Purpose
The Kyowa Kirin Group will contribute to the health and well-being of people around the world by consistently providing world-class quality pharmaceutical products and services in compliance with our global quality, safety and compliance policies.
This policy is to describe the basic principles for quality of the Kyowa Kirin Group.
2. Scope of Application
This policy applies to all personnel including officers and employees of the Kyowa Kirin Group. The Kyowa Kirin Group will request all of our business partners and agents engaged in our products and services to act in accordance with the basic principles stated in this policy.
3. Definition of Terms
- GxP means GLP (Good Laboratory Practice), GCP (Good Clinical Practice), GMP (Good Manufacturing Practice), GQP (Good Quality Practice), GDP (Good Distribution Practice) and GVP (Good Vigilance Practice).
- Quality management system is a formalized system that documents processes, procedures, and responsibilities for achieving quality policies and objectives.
4. Basic Principles
We will act in accordance with the following basic principles.
- Compliance and Continuous Improvement
- We conduct our business in compliance with all global laws, regulations, and guidelines related to GxP. To ensure compliance, we will continuously improve our quality management system.
- Cooperation and Collaboration with Stakeholders
- We maintain sound relationships with regulatory authorities, suppliers, and contractors around the world to ensure a continuous supply of high-quality pharmaceutical products.
- Predictive and Preventive Quality Assurance
- We strive to prevent problems before they occur by using information and digital technologies to proactively identify and address risks.
- Fostering a Quality Culture
- We foster a healthy Quality Culture in our organization, openly discussing issues, and collaborating with our teams to ensure that we always act with integrity from the patient's perspective.
Governance
Global QA Vision and Mission
We contribute to patients by following our Vision and executing our Mission.
Our Vision is to lead in Quality by fostering a culture of continuous improvement and innovation across all processes, systems, and products, enabling us to deliver life-changing value and bring smiles to our patients.
Our Mission is to assure safe, effective, and high-quality products and services by executing our strategic Global Quality Roadmap. We are committed to quality, compliance, and integrity, empowering our teams to create value for stakeholders and build trust with our patients.
A Quality Culture is centered around three key components: establishing a clear vision, fostering a set of shared values that all employees embody, and providing strong leadership. In a healthy Quality Culture, you will find science-based decision-making, effective risk management, robust data integrity, compliance, a supportive management structure, a proactive approach to preventing issues before they arise, and a mindset focused on continuous improvement.
Our ultimate goal, as part of our Global Quality Roadmap, is to achieve a competitive advantage by developing a world-class Quality System and nurturing a strong Quality Culture.
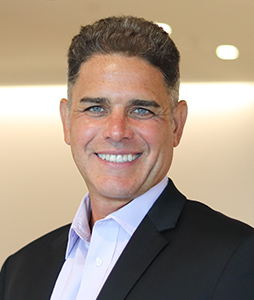
Jonathan Patroni
Organization for Global Quality Assurance
As illustrated in the figure below, the Global Quality Assurance function is structured so that the Global Quality Head reports directly to our Chief Compliance Officer (CCO). The Global Quality Head oversees all Quality Assurance activities across regions, including JAPAC, North America, and EMEA, as well as all Global QA functions. Regional QA groups collaborate closely with the five Global QA functions, which possess high levels of expertise, to ensure a globally consistent structure for Quality Assurance and oversight. Our Global Quality Assurance framework has been designed and implemented with the highest priority on patient safety, compliance, and customer satisfaction.
Specific Initiatives
Quality Risk Management
Kyowa Kirin regularly convenes Global Product Council meetings to review global product initiatives and quality data. This enables us to identify product quality issues early and determine preventive measures to mitigate the risk of non-compliant products and unstable supply, with patient safety as our top priority. We have established a robust process for escalating quality incidents to senior management and promptly convene ad hoc Global Product Council meetings to discuss risk-based mitigation actions based on impact and root cause assessments.
We adopt a systematic approach to the comprehensive management of drug product and drug substance quality risks by assessing, controlling, communicating, and reviewing risks throughout the product lifecycle. Additionally, we recognize that strengthening predictive and preventive quality assurance is a key initiative; therefore, we actively monitor comprehensive quality risks using quality risk registers.
Employee Quality Training
Kyowa Kirin is dedicated to fostering a culture of quality by regularly conducting quality-related training for all employees. During Global Quality Month in November, we engage in activities that promote a unified quality culture and organize events across each region to raise awareness of quality and compliance.
Supplier Management
To ensure and maintain the high standards of quality we require, we establish comprehensive manufacturing and quality agreements with all our contractors, regularly reviewing their implementation status. Additionally, we provide quality training specific to each supplier's risk level and support improvement initiatives through regular review meetings.